日時 | 2017年10月6日(金曜日)10時〜11時45分 |
視察先 | 川崎重工業株式会社 播磨工場(兵庫県 加古郡) |
参加者 | 19名(EPOC会員) |
目的 | 川崎重工業の水素サプライチェーンのコンセプトについて学び、実現の核となる技術のひとつである、「水素液化プラント」と水素関連製品について見学する。 |
所感 | 水素サプライチェーンのコンセプトのスケールの大きさに圧倒された。水素社会の到来はまだまだ先のことと考えていたが、具体化された技術・施設を見学することで、実現に向かって力強く動いていると感じた。 |
1.施設概要
播磨工場は瀬戸内海に面した播磨工業地帯のほぼ中央に位置する人工島で、45万m2の敷地を有する。1971年に開設され、現在はプラント・環境保全設備、ボイラ、土木建設機械、鉄構等を生産している。
2.事業紹介(「水素サプライチェーンの実現に向けた取組み」)
(1)企業概要
川崎重工業は総合メーカーであり、一般消費者向けにはモーターサイクル、ほかに輸送分野では船舶や鉄道車両、エネルギー分野でガスタービン・エンジンなど、また各種プラントや環境分野ではごみ焼却場などを手掛けている。さらに精密機械として油圧ポンプやラジエーター、ほかにロボット等を作っている。
水素関連で主なものは、種子島H-IIロケット基地(液化水素貯蔵タンク)で約30年前からトラブルなく稼働している。貯蔵されている一価水素は岩谷産業が製造。ほかに液化水素輸送コンテナなどがある。圧縮水素トレーラー等は水素ステーションで需要があり、手がけている。直接的ではないが肥料プラントの工程で大量に水素を製造するものもある。
(2)エネルギーを取り巻く状況
2015年12月COP21のパリ協定で世界は低炭素から脱炭素へシフトした。世界的な平均気温上昇を産業革命前に比べて2℃のみならず、1.5℃に抑える努力をすることを謳い、米中含め100か国が批准した。日本のCO2削減目標は、2030年までに26%削減、2050年までには50%減。特に2050年の50%減は、これまでの延長では達成できない高い目標で、ドラスティックにやり方から変えていかなくてはならない。
(3)水素利用への動き
水素は産業ガスとしては一般的に使われてきたが、エネルギーとしての利用は、2014年に「エネルギー基本計画」で水素利用が初めて大きく記載されたことに端を発する。これを受けて経産省はロードマップを策定し、「未利用資源褐炭からの水素製造」や「水素発電」が明記された。
水素・燃料電池戦略ロードマップのフェーズ1は、エネファームの自立化やMIRAIなどFCV用水素ステーションの設置などを進めることが掲げられている。同社はフェーズ2(大規模水素供給システムの確立)に関連している。水素利用の飛躍的拡大により、大量に水素が必要になるため、供給側として安定的に低価格で提供するためにはどうしたらよいか、を手掛けている。水素の大量供給が実現すればフェーズ3として、2040年ごろに水素供給システムが確立される。
現在はプロセス用途の水素需要がメインで、半導体製造や脱硫など化学反応として水素が利用されている。さらに2010年のトヨタ自動車のMIRAI発売に象徴されるように、輸送機セクターでも水素が使われるようになってきた。東京オリンピックが「水素オリンピックに」と言われているように、最終的に発電用途としての水素が必要になってくる。
今年の施政方針演説で、安倍首相は水素エネルギーの重要性を強調した。同社に関わることとしては、「神戸での水素発電による世界初の電力供給」および「世界初の液化水素船による大量水素輸送への挑戦」も明記された。更に、これまでの「再生可能エネルギー等関係閣僚会議」という名称に「水素等」が加えられた「再生可能エネルギー・水素等関係閣僚会議」では、国際的な水素サプライチェーンの構築には水素発電が重要と示され、これを受けて今年中に関係省庁(経産省、環境省、国交省、文科省等)が青写真を作る準備をしている。
グローバル企業の動きとして「Hydrogen Council」がある。これはエネルギー・運輸・製造業の世界的なリーディングカンパニー13社のCEOクラスが集まり、水素利用を世界的に啓蒙していこうという集まりである。2017年の1月にはスイスのダボスで開かれた世界経済フォーラムで設立が発表された。当初は13社であったが、その後日本の岩谷産業、アウディ、GM等が加わっている。次回は2017年11月にドイツ・ボンで開かれるCOP23で集まる予定である。
(4)水素サプライチェーンのコンセプト
水素は様々な化合物に含まれ、これを化学変化させて取り出す。例えば水の電気分解により、あるいは天然ガス(主成分はメタン(CH4))から取り出すなど様々な方法がある。同社が着目したのは、オーストラリアの褐炭を利用し、水素を生成する方法である。まず水素を作り出し、それを現地で液化して輸送貯蔵し、最終的に利用する。大量に運ぶために液化するという方法は、天然ガス(LNG)でも使われている。
褐炭は石炭の一種なので、水素生成時にどうしてもCO2が出てしまうため、現地でCCS(Carbon Capture Storage)により貯留してCO2フリーの形にしている。褐炭は若い石炭で、数千万年くらいのものである。(黒光りしている無煙炭等の石炭は数億年。数百年は泥炭。)種類が異なるわけではなく、年齢が異なるだけで、世界に広く分布しており、水分量が多く輸送効率が悪い。しかし乾燥させると自然発火しやすいため輸送が困難である。したがって従来は現地で使うしかなかった。採掘権のみの未利用資源で安価であり、権益取得が容易であるといった理由から、同社は褐炭を選んでいる。
褐炭は、豪州の首都メルボルンから東に150kmにあるラトロブバレーで露天掘りされている。すぐそばには褐炭発電所があり現地で使われている。ビクトリア州の約8割の電力がここで賄われている。
ここには日本の総発電量の240年分に相当する褐炭が賦存している。
オーストラリアの連邦政府とビクトリア州政府はCCSプロジェクト「Carbon Net」を推進している。最終的には、ラトロブバレーから80kmのパイプラインを介してCO2を持ってきて貯留する。ポーランドやドイツなどヨーロッパでも褐炭が多く出るところはあるが、CCSが可能な場所は少ない。
輸送のキャリアとして、有機ハイドライドで運んだり、アンモニアで運んだりという方法があるが、同社は液化水素を選択している。その主な理由は、液化水素は生産過程で非常に高純度になるため、日本に持ってきた際に精製が不要で、蒸発させるだけで使用可能なためである。国内の電気エネルギーは高価であり、また火力発電が中心のため、発電時CO2排出量が多い。国内にて電気を使い精製をするとコストは不利となり、水素製造時のCO2排出量が増加してしまい、CO2フリー水素と評することが難しくなってしまう。一方で、-253℃で液化する点でハードルが高いが、同社は30年前から必要なタンクや技術などを有してきた。LNG船も有しており、-163℃の低温技術も持っている。
更に水素を一日770t製造して日本に運んでくる規模にてコスト評価を行っている。770tは大きな火力発電所一機分(100万kW)またはFCV300万台の燃料に相当する量である。この想定のもと、船で運んでくるまでの費用(CIFコスト)を約30円/Nm3とはじき出している。水素ステーションに持ってくるまでの費用も含めると約60円/Nm3となる。現在の水素ステーションでは100〜110円/Nm3で販売されているため、原価60円であれば対抗できると試算している。30円の内訳のうち、水素製造〜水素運搬船までは日本の技術・製品を活用することができ、日本の産業の育成にも寄与できる。例えばLNGは約7〜8割が燃料代で、欧米が技術ライセンス等を持っているため、どうしても利益が海外に流出してしまう。それに比べ水素は理想的なコスト構造となっている。
LNGの歴史から将来の水素導入シナリオ(ポテンシャル)を予測している。その予測によれば、液化水素の輸入基地が日本に沢山できてくれば(2050年に40基地、1つの基地に2隻で80隻規模になると)値段も18円/Nm3まで下がってくる。発電コストは2030年の初期で16円/kWh程度。このコストにCCSも含まれている。2050年になると量が増える効果で11円/kWhを想定している。2050年に原子力など他の発電コストがどうなっているかはわからないが、他の燃料と競合できるレベルに達すると考えられる。
このプロジェクトは日本だけでなく、オーストラリア側にとってもメリットがある。輸出できなかった資源をクリーンエネルギーとして輸出できる上、雇用も創出でき、オーストラリア政府とはWin-Winの関係になっている。
(5)技術開発状況
川崎重工の水素関連技術のなかでも特に注力しているのが、世界初の液化水素運搬船で、大きな魔法瓶のような真空断熱二重殻構造を持つ。ただし、液化水素を運搬する船舶に関するレギュレーションが存在しなかったため、液化水素を運ぶためのガイドラインを国交省がIMO(国際海事機関)に提案し、2016年のロンドンの会合で審議され、承認された。これによりこの液化水素運搬船を用いた世界初の国際間液化水素取引を実施することが可能となった。
今後の展開としては、2018年に神戸で世界初の水素ガスタービンコージェネレーションの建設、運転を予定し、2020年までに日豪水素サプライチェーンのパイロット実証を行うこととしている。
ガスタービンコージェネでは、水素炊きのガスタービン(1MW級)で地域にエネルギーを供給する世界で初めての取組みを実施している。このガスタービンは水素と天然ガスの混焼だけでなく水素100%の専焼にも対応している。
パイロット実証の具体的実施項目としては、オーストラリアにて褐炭を用いた水素製造プラントの建設及び実証運転、液化水素運搬船の建造及び実証運転、液化水素荷揚基地の建設及び実証運転を行う計画である。これらはNEDOの補助事業として行われるとのことであった。
また、パイロット実証を遂行するために、電源開発、岩谷産業、シェルジャパンと技術研究組合(HySTRA:ハイストラ)を設立している。褐炭から水素をつくる部分は電源開発が担当し、船や基地をつくる部分は川崎重工業や岩谷産業、シェルジャパンが担当している。岩谷産業やシェルジャパン(世界で最もLNG船を運航している)はオペレーターの視点で協力している。
この他に、NEDO事業にて豊田通商が幹事となった、北海道の苫前で風力発電由来電力から水電解を用いて水素を製造し、貯蔵、輸送、利用を含めたPower to Gasシステムの開発実証事業にも参加している。
以上をまとめると、CO2フリー水素チェーンの主な意義・効用は、供給安定性、環境性、産業競争力向上である。
3.施設見学
(1)水素液化プラント
水素サプライチェーンの「つくる」「ためる」にあたる技術が、「水素液化プラント」である。プラントでは1日あたり約5トンの水素を液化する能力を有している。本システムは、水素液化機、液化した水素を貯蔵する液化水素貯蔵タンクなどで構成されている。本システムは、純国産の独自技術で開発したもので、極低温物質のハンドリング技術や高速回転機械の開発で培ったタービン技術が活用されている。
同システムでは、圧縮した水素ガスを冷凍サイクルで冷やされた水素と液化機内で熱交換しながら冷却することで液化水素を製造する。
水素は液化すると体積が約800分の1になり、利用の際は蒸発させるだけで高純度の水素ガスを得ることができる。ただし、液化水素はLNGの10倍蒸発しやすいため、長期保存のためには、タンク内での液化水素の蒸発を抑えることが重要である。同社ではLNG貯蔵タンクより高度な断熱技術を開発して液化水素貯蔵タンクを実現している。
(2)水素技術実証センターおよび水素関連製品
「ためる・はこぶ」にあたる部分として、水素運搬船がある。水素を次世代エネルギーとして活用するためには、大量の水素を効率よく、安全に輸送する技術が求められる。同社は日本で初めてマイナス162℃でLNGを運ぶ運搬船を建造したが、液化水素はそこから更にマイナス100℃近く低く、蒸発しやすい。そのため、液化水素を貯蔵するタンクには真空二重殻構造及び積層断熱材という断熱技術が使われている。また、新素材の使用だけでなく、タンクの曲線を作る曲げ加工や、隙間ない溶接加工など、職人の技術も合わさって、世界最大の真空魔法瓶ともいうべき液化水素貯蔵タンクはでき上がっている。
また、液化水素を陸上で大量に輸送するためのコンテナ車や、多様な輸送形態のニーズに応えて圧縮水素トレーラーも製造している。
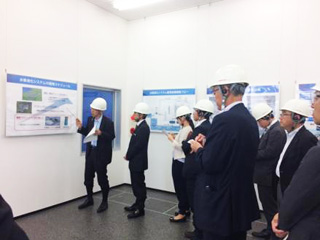
水素技術センターにて説明を受ける
4.質疑応答
Q 一部海外の技術・部品・設備を使わなければならない理由は何か。水素設備に特化したため必要となるのか。
A 一部分だけ日本で製作できないため、海外製品を持ってくるしかない。これは弱点であり、やめたいと思っている。
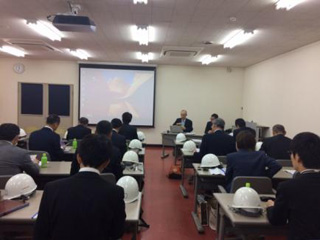
質疑応答
Q コスト面で、30円/Nm3を切りたいとのことだが、生産量以外でブレイクスルーが必要となるモノはなにか。
A 一番は液化にかかる電気。液化動力の効率化が大きいと見込んでいる。また、水素製造時のCO2分離の効率化も重要と考えている。
Q CCSのような複雑な設備があるが、単純に水を電気分解した方が早いような気がしてしまう。
A 水電解というのはCO2を排出しないので究極的にクリーンではある。ただし、大規模な水電解装置がない、また再生可能エネルギーのコストが高い。水電解は電力がもろにコストに反映するので、再生可能エネルギーから水素を作るのは割に合わない。通常の電力なら割に合うかもしれないが、CO2を出すのでそれをどのように扱うかが悩みどころとなっている。まずは化石燃料から低コストで水素を製造することを目指し、最終的には再生可能エネルギーから水素を低コストで作れるように研究を続けている。車レベルの小規模なものなら水電解でも可能だが、大量の水素を使って再生可能エネルギーにするにはまだ時間が必要である。
Q ドイツの企業が液化技術の特許を取得したが、その特許のライセンスに触れたりしたのか。あるいは回避するために何かオリジナルのもので突破したのか。
A 特許侵害にならないように自社でオリジナルの技術を開発した。
Q なぜ今まで水素事業への着手を行わなかったのか。
A 液化水素の市場が小さいので莫大な投資をしてもリターンが見込めなかった。2013年から手掛けたのは将来を見据えての行動である。
Q タンクの配管の溶接等、最終的にヒトの技術によるものがあるが、社員間での技能伝承等はあるのか。
A いくら機械化ができたとしても人の手は必要。技能のあるベテラン世代が退職していくため、若手に技術伝承をするため「技能道場」などを使って継承できるようにしている。